
Warehouse and industrial properties require expansive yet efficient storage and space solutions. Because of their versatile flexibility, steel and metal warehouse buildings have emerged as the gold standard for industrial and commercial warehousing and manufacturing facilities across the Southern United States. From metal warehouses in Texas to steel manufacturing buildings in Louisiana, Arkansas, and Oklahoma, these structures are revolutionizing the way businesses approach their storage and operational needs.
Durability and Strength
Steel building systems and metal building systems offer unparalleled durability and strength. In harsh climates like those found in Texas and Louisiana, steel warehouses stand strong against severe weather conditions. Metal warehouses in Arkansas and Oklahoma provide lasting protection for valuable inventory and equipment. The structurally sturdy nature of steel warehouse construction across the South ensures that these structures can withstand the test of time, offering businesses a long-term solution for their storage needs.
Cost-Effectiveness
When it comes to cost-effectiveness, metal warehouse manufacturers in Texas and throughout these Southern states are leading the charge. The efficiency of pre-engineered metal building systems in Louisiana and turnkey steel warehouses in Texas significantly reduces construction time and labor costs. Metal warehouse building systems in Arkansas and Oklahoma offer an affordable option for businesses looking to expand quickly. The long-term savings on maintenance and energy efficiency make steel and metal warehouses a cost effective investment for companies across the region.
Flexibility and Customization
One of the most significant advantages of steel and metal building systems is their incredible flexibility. Custom steel warehouses can be designed to meet specific business needs, while prefabricated metal warehouses offer quick and easy setup. Industrial steel building systems provide versatile spaces that can adapt to changing business requirements. Commercial metal warehouses can be easily modified or expanded as businesses grow.
Steel building contractors and metal building manufacturers across the South specialize in creating tailored solutions. Whether it's warehouse steel frames or custom commercial steel buildings, these experts can design structures that perfectly align with your operational needs. Just look for “warehouse metal building systems near me” to find a metal building manufacturer that can create your warehouse or industrial space optimized for efficiency.
In East Texas, Tyler Building Systems is a “warehouse metal building systems near me” manufacturer that designs, manufactures, and delivers metal warehouse and industrial manufacturing spaces with the strength of steel and versatility of a custom designed metal structure.
These warehouse metal buildings offer the perfect blend of capability, cost-effectiveness, and customization, making them the ideal choice for businesses looking to invest in their future. As the demand for efficient storage solutions continues to grow, steel and metal warehouses will undoubtedly remain at the forefront of industrial and commercial construction across the South.
Steel and Metal Warehouse Manufacturing is a Southern Regional Powerhouse
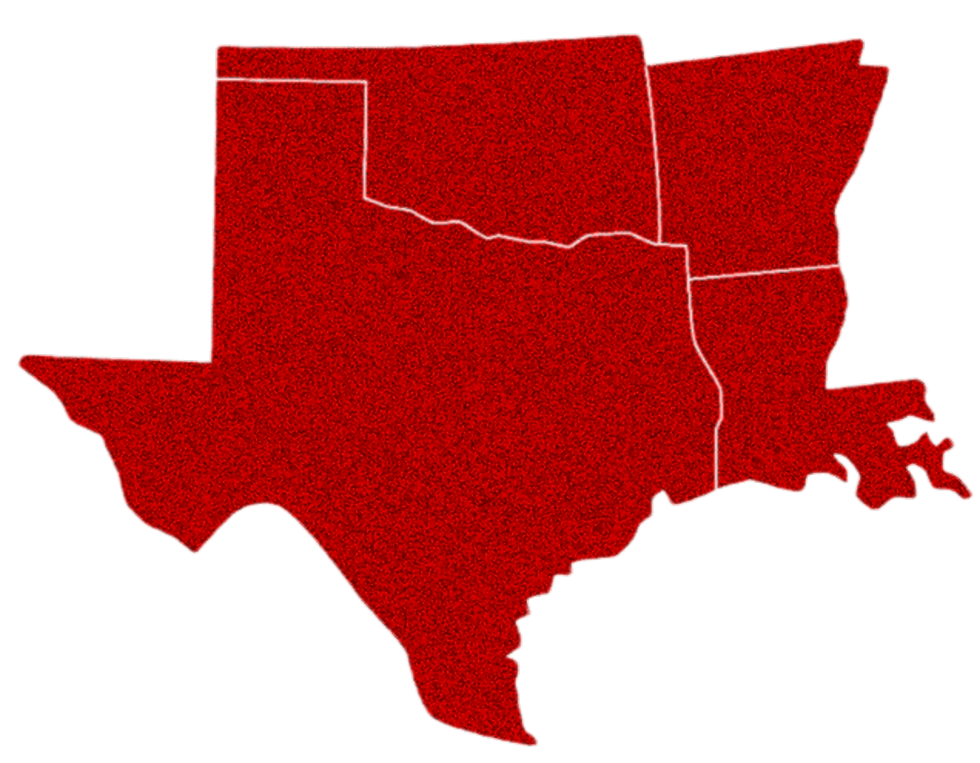
The Southern United States has become a hub for innovative industrial and commercial spaces, with steel warehouses and metal warehouses leading the charge. Wth the regional availability of steel building systems and metal building systems across Texas, Louisiana, Arkansas, and Oklahoma, there are unique offerings and advantages in each state.
Texas: The Lone Star State of Steel
Texas stands at the forefront of the steel and metal building revolution. With its vast geological riches and booming economy, the demand for steel warehouses in Texas has skyrocketed. Steel building systems in Texas cater to a wide range of industries, from oil and gas to technology and agriculture.
Custom steel warehouses in Texas are particularly popular, offering businesses tailor-made solutions to meet their specific needs. Warehouse metal building systems companies in Texas are known for their innovative designs and cutting-edge technology. For those seeking faster and more affordable construction solutions, steel and metal warehouses in Texas provide an efficient and effective option.
Steel warehouse manufacturers in Texas have established a reputation for quality and reliability. Their expertise in creating durable structures capable of withstanding the state's diverse climate conditions has made them industry leaders. For businesses looking to expand or establish new facilities, Texas has a large network of suppliers, manufacturers, and contractors.
To find "warehouse metal building systems near me" in Texas, look to Tyler Building Systems or contact us here.
Louisiana: Where Tradition Meets Innovation
Louisiana's manufacturing and industrial needs have created a thriving market for metal warehouses and steel building systems. Metal warehouses for Louisiana are designed to withstand the state's humid climate and occasional severe weather, making them ideal for long-term storage and industrial use.
Prefabricated metal warehouses have gained popularity due to their quick installation and cost-effectiveness. These structures are perfect for businesses looking to expand rapidly without compromising on quality. Pre-engineered metal building systems offer a balance of efficiency and customization, allowing companies to create spaces that perfectly align with their operational requirements.
Metal warehouse manufacturers serving Louisiana have developed expertise in providing solutions for different industries, including petrochemical, agriculture, and logistics.Warehouse building solutions in Louisiana often incorporate advanced features to enhance energy efficiency and durability, reflecting a commitment to sustainable development.
Tyler Building Systems is known for manufacturing metal building systems with American steel, adapted to the diverse needs of Louisiana's dynamic economy.
Arkansas: The Natural State's Steel Revolution
Arkansas has embraced steel and metal building systems as a cornerstone of its industrial and commercial development. Steel warehouses delivered and erected in Arkansas are renowned for their durability and adaptability, catering to the state's diverse economic sectors.
Industrial steel building systems in Arkansas have transformed the manufacturing and logistics landscapes. These structures offer expansive, unobstructed spaces ideal for large-scale operations. Steel warehouse construction in Arkansas is characterized by its efficiency and precision, with projects often completed in record time.
Steel building contractors in Arkansas have honed their skills to deliver exceptional quality and service. Their expertise in creating warehouse steel frames ensures that each structure is built to last, capable of supporting heavy loads and withstanding various environmental challenges.
Tyler Building Systems manufactures custom metal warehouses in Arkansas showcase the state's commitment to innovation, with designs that blend functionality with aesthetic appeal.
Oklahoma: Where Metal Meets Possibility
Oklahoma's growing economy has fueled a surge in demand for commercial and industrial spaces, with metal building systems taking center stage. Metal warehouses in Oklahoma are favored for their versatility and cost-effectiveness, serving a wide range of industries from energy to aerospace.
Commercial metal warehouses in Oklahoma have become a staple for businesses looking to expand their operations. These structures offer the flexibility to create multi-purpose spaces, from retail showrooms to offices to distribution centers. Metal building systems manufactured for Oklahoma businesses provide an accessible option for smaller businesses or those looking to manage their construction projects. Optimized for efficiency and functionality, commercial steel buildings in Oklahoma often incorporate state-of-the-art features, reflecting the state's forward-thinking approach to industrial development.
Metal building manufacturers serving Oklahoma, like Tyler Building Systems, have developed a reputation for excellence, offering comprehensive services from design to construction.
Tyler Building Systems serves Oklahoma with a reputation for excellence, offering comprehensive services from design to construction.
Across Texas, Louisiana, Arkansas, and Oklahoma, the steel and metal warehouse industry continues to thrive, driven by innovation, quality, and a deep understanding of regional needs. Whether you're looking for a custom solution in Texas, a prefabricated option in Louisiana, an industrial powerhouse in Arkansas, or a versatile commercial space in Oklahoma, the Southern United States offers a wealth of options in steel and metal building systems. As these states continue to grow and evolve, steel and metal warehouses will undoubtedly play a crucial role in shaping the future of industrial and commercial spaces in the region.
The Evolution of Storage: Steel and Metal Warehouses

Steel and metal warehouses have become the backbone of modern storage solutions. From the bustling cities of Texas to the rural expanses of Arkansas, stretching into Oklahoma and Louisiana, these structures are revolutionizing how businesses approach their storage needs. Explore the three primary types of steel and metal warehouses dominating the market: prefabricated metal warehouses, custom-engineered warehouses, and modular warehouses.
Prefabricated Metal Warehouses
Prefabricated metal warehouses, also known as pre-engineered metal building systems, are structures designed and manufactured off-site, then assembled on location. This type of construction has gained significant popularity, especially in Southern states, where efficiency and cost-effectiveness are king.
The benefits of prefabricated metal warehouses are numerous:
Rapid Construction: Prefabricated metal warehouses can be erected in a fraction of the time required for traditional construction methods.
Cost-Efficiency: With most components manufactured in controlled environments, labor costs and material waste are significantly reduced.
Consistency: Each component is precision-engineered, ensuring a high level of quality and uniformity.
Flexibility: These structures can be easily expanded or modified to accommodate changing business needs.
Metal warehouse manufacturers have perfected the art of delivering these efficient structures, making them a go-to choice for businesses looking to expand quickly without compromising on quality.
Prefabricated metal warehouses are versatile and can be adapted for various uses:
Storage Facilities: Ideal for businesses needing large, open spaces for inventory management.
Distribution Centers: The quick assembly time makes them perfect for rapidly expanding logistics operations.
Multi-use Office and Storage: Businesses often opt for these structures to protect inventories and run office operations.
Retail Spaces: Some businesses use these as cost-effective solutions for large showrooms or outlets.
Custom-Engineered Warehouses
Custom-engineered warehouses represent the pinnacle of metal building systems. These structures are designed from the ground up to meet specific business requirements. Steel warehouse manufacturers in Texas are at the forefront of this trend, creating highly-tailored solutions that push the boundaries of what's possible with metal construction.
The benefits of custom-engineered warehouses include:
Tailored Design: Every aspect of the building can be customized to fit unique operational needs.
Optimal Space Utilization: Custom designs ensure that every square foot serves a purpose.
Integration of Specialized Equipment: The structure can be designed to accommodate specific machinery or processes.
Aesthetic Flexibility: Custom metal warehouses can be designed to match corporate branding or local architectural styles.
Steel building contractors working alongside metal building manufacturers have embraced this approach, offering businesses the opportunity to create truly unique spaces that perfectly align with their vision and requirements.
Custom-engineered warehouses find applications in various industries:
Manufacturing Facilities: Companies can design spaces that optimize production flow and integrate complex machinery.
Research and Development Centers: These warehouses can be engineered to include specialized laboratories and testing areas.
Multi-Use Commercial Spaces: Businesses can create hybrid spaces that combine storage, office, and retail under one roof.
Specialized Industrial Facilities: Industries with unique requirements, such as aerospace or pharmaceuticals, often opt for custom solutions.
Modular Warehouses
Modular warehouses represent a blend of prefabrication efficiency and custom design flexibility. These structures are composed of pre-engineered sections or modules that can be assembled in various configurations. This approach has gained traction across the South, where businesses value adaptability and scalability.
Key benefits of modular warehouses include:
Scalability: Businesses can start with a smaller structure and easily add modules as they grow.
Reconfigurability: The modular nature allows for easy redesign of internal spaces as needs change.
Portability: In some cases, these structures can be disassembled and relocated, offering ultimate flexibility.
Adaptability: While offering more customization than standard prefab options, modular warehouses still boast quick assembly times.
Metal building companies have embraced this innovative approach, offering businesses a middle ground between off-the-shelf solutions and fully custom designs.
Modular warehouses are particularly suited for:
Temporary or Seasonal Storage: Businesses with fluctuating storage needs can easily scale up or down.
Disaster Relief and Emergency Response: Quick deployment makes these ideal for setting up temporary facilities in crisis situations.
Pop-Up Retail or Event Spaces: The ability to quickly assemble and disassemble makes them perfect for short-term commercial use.
Educational Facilities: Schools and universities use modular structures for flexible classroom or laboratory spaces.
Regional Trends and Innovations
As we look across the Southern United States, we see distinct trends emerging in the steel and metal warehouse industry:
In Texas, the demand for warehouse metal buildings near me has surged, with businesses prioritizing local suppliers for quicker turnaround times. Warehouse metal building systems companies in Texas are innovating with smart technology integration, creating structures that are not just storage spaces but intelligent assets in a company's operations.
Louisiana has seen a rise in the adoption of warehouse building systems that prioritize energy efficiency and hurricane resistance. Warehouse building solutions in Louisiana often incorporate advanced insulation and reinforced structures to withstand the state's challenging climate.
Arkansas is experiencing a boom in industrial steel building systems, particularly in the state's growing logistics and manufacturing sectors. Steel warehouse construction in Arkansas is increasingly focused on creating multi-purpose facilities that can adapt to changing economic conditions.
In Oklahoma, there's a growing trend towards commercial steel buildings that blend functionality with aesthetic appeal. Metal warehouse design in Oklahoma is evolving to create structures that not only serve their primary purpose but also enhance the visual appeal of industrial and commercial areas.
Tyler Building Systems delivers quality materials, custom designed metal building systems, and trusted expertise for your next metal building project.
The landscape of steel warehouses and metal warehouses across Texas, Louisiana, Arkansas, and Oklahoma is diverse and dynamic. From prefabricated metal warehouses offering quick solutions to custom-engineered marvels pushing the boundaries of design, and modular structures providing unparalleled flexibility, the options are vast and varied.
As businesses continue to evolve, so too will the steel and metal building systems that support them. Whether you're looking for turnkey steel warehouses in Texas, exploring pre-engineered metal building systems in Louisiana, considering steel warehouse construction in Arkansas, or investigating metal warehouse kits in Oklahoma, the future of industrial and commercial spaces in the South is bright, efficient, and built on a foundation of steel and innovation.
Key Features of Steel & Metal Warehouses
In industrial and commercial construction, steel warehouses and metal warehouses have emerged as the preferred choice for businesses across the Southern United States. From steel warehouses in Texas to metal warehouses in Louisiana, Arkansas, and Oklahoma, these structures offer unparalleled benefits in terms of durability, flexibility, and cost-effectiveness. Let's explore the key features that make steel and metal building systems the cornerstone of modern warehousing solutions.
Structural Components
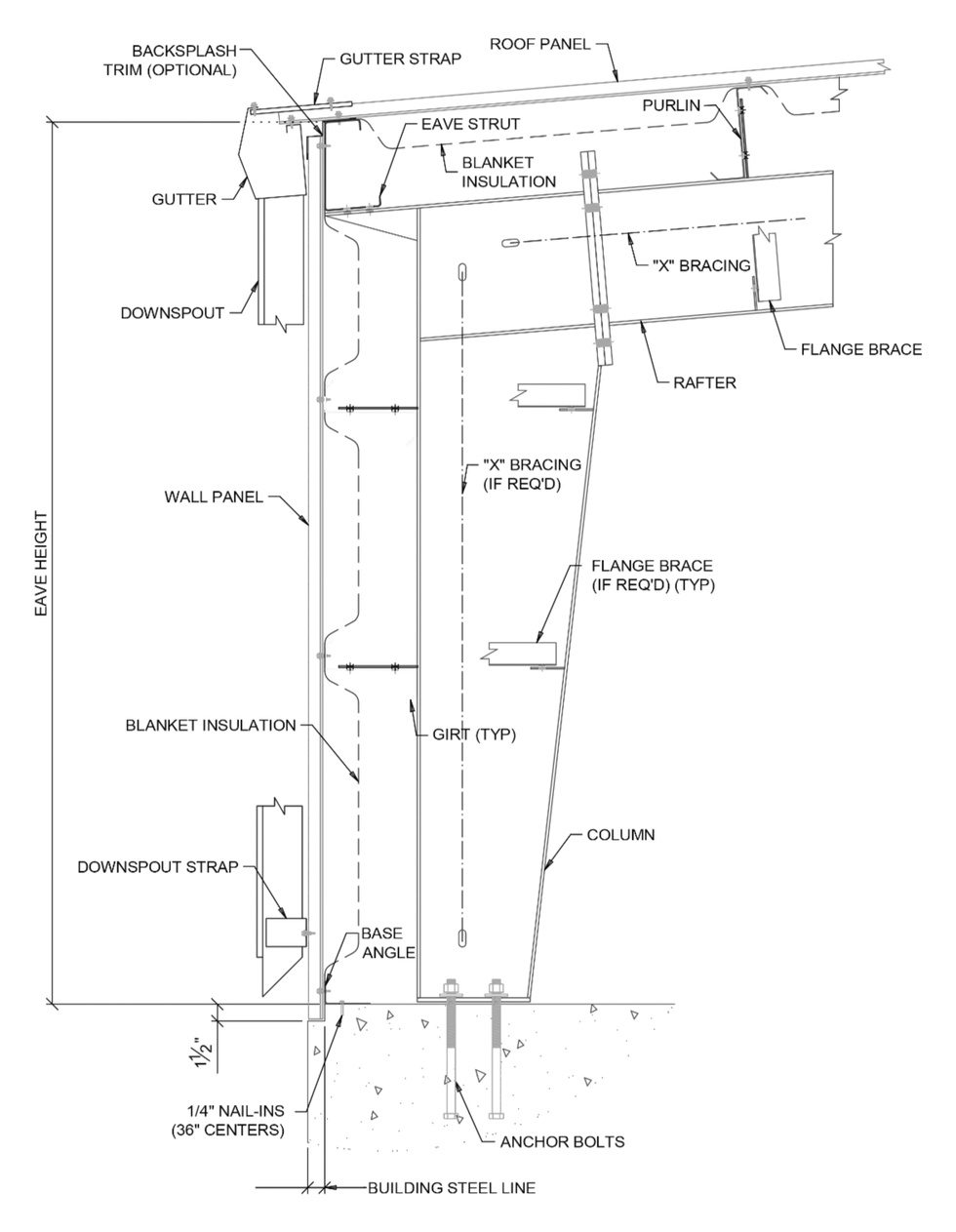
Frames and Supports
The backbone of any steel or metal warehouse is its structural frame. Metal building systems utilize advanced engineering techniques to create robust, yet lightweight frames. These frames, often made from high-strength steel, provide the necessary support to withstand heavy loads and resist environmental stresses.
Warehouse steel frames are designed to offer maximum clear span, allowing for optimal use of interior space. Steel warehouse manufacturers are pioneering the use of advanced alloys that offer increased strength-to-weight ratios, enabling the construction of larger, more efficient structures.
Roofing Systems
The roofing system is crucial for protecting the contents of industrial warehouses and commercial warehouses. Metal building systems often feature standing seam metal roofs, known for their excellent weather resistance and longevity. These roofs can be engineered to support solar panels, enhancing the structure's energy efficiency.
In locations where heavy rainfall is common, metal warehouses are equipped with sophisticated gutter and downspout systems to manage water effectively. Some warehouse metal building systems companies are now offering cool roof options that reflect sunlight, reducing cooling costs in the hot summer months.
Insulation and Climate Control
Proper insulation is essential for maintaining a controlled environment within steel and metal warehouses. This is particularly crucial for businesses dealing with temperature-sensitive goods or equipment. In Southern states, where temperature fluctuations can be extreme, effective insulation can significantly reduce energy costs and protect inventory.
Modern steel building systems offer a range of insulation options. Blanket insulation is commonly used in prefabricated metal warehouses in Louisiana, providing a cost-effective solution for basic climate control. For more demanding applications, spray foam insulation is gaining popularity, especially in custom steel warehouses, offering superior R-value and air sealing properties.
Warehouse building solutions often incorporate reflective insulation to combat the intense summer heat. In colder regions, steel warehouses may use a combination of insulation types to create a highly efficient thermal envelope.
Customization Options
The true strength of metal building systems lies in their flexibility. Custom steel warehouses can be designed to meet specific business needs, while prefabricated metal warehouses offer quick and cost-effective solutions. Size and layout can be tailored to fit any requirement, from small storage units to massive distribution centers.
Metal building companies specialize in creating structures with versatile door, window, and ventilation options. From large rolling doors for easy access to strategically placed windows for natural lighting, every aspect can be customized. Interior partitioning and mezzanines in commercial metal warehouses allow businesses to maximize their space utilization. The key features of steel and metal warehouses offer a perfect blend of strength, efficiency, and adaptability for businesses across the South.
Size and Layout
One of the most significant advantages of steel and metal building systems is their incredible flexibility in terms of size and layout. Metal building contractors can design structures ranging from smaller commercial storage units to massive distribution centers. The clear-span capabilities of steel frames allow for expansive, column-free interiors, maximizing usable space.
Metal building companies offer modular designs that allow for easy expansion as businesses grow. This scalability is particularly attractive for startups and rapidly expanding enterprises.
Doors, Windows, and Ventilation
Customization extends to every aspect of the warehouse, including doors, windows, and ventilation systems. Commercial metal warehouses can be equipped with a variety of door types, from standard roll-up doors to specialized high-speed doors for high-traffic areas.
In states like Texas, Oklahoma, Louisiana, and Arkansas, where natural light is abundant, warehouse metal buildings often incorporate skylights or translucent wall panels to reduce reliance on artificial lighting. Ventilation systems can be tailored to specific needs, with options ranging from simple ridge vents to sophisticated HVAC systems for climate-controlled environments.
Interior Partitioning and Mezzanines
The versatility of steel and metal warehouses allows for endless interior configurations. Industrial steel building systems can be designed with movable partitions, enabling businesses to adapt their space as needs change. Mezzanine floors are a popular addition in many commercial steel buildings, effectively doubling usable space without increasing the building's footprint.
Metal warehouse design has evolved to include innovative storage solutions, such as vertical lift modules and automated storage and retrieval systems, seamlessly integrated into the building's structure.
From prefabricated steel warehouses to pre-engineered metal building systems, the key features of steel and metal spaces for industrial use offer businesses unparalleled flexibility, efficiency, and durability. As technology advances and business needs evolve, these structures will continue to adapt, cementing their position as the future of industrial and commercial spaces across the United States.
Construction and Installation Process
The journey from concept to completion for steel warehouses and metal warehouses is a meticulously planned process that ensures the highest quality and efficiency. Whether you're looking at steel warehouses in Texas or metal building systems in Oklahoma, understanding the construction and installation process is crucial for a successful project.
Planning and Design
The process begins with a comprehensive consultation. Steel warehouse manufacturers and suppliers work closely with clients to understand their specific needs. This initial phase is critical for custom metal warehouses, where unique requirements often drive the design.
Metal building manufacturers like Tyler Building Systems employ advanced CAD software to create detailed designs for warehouses and industrial metal building systems, integrating specialized equipment and workflow considerations into the building's layout.
Permitting and Regulations
Each state has its own set of building codes and regulations. Steel building contractors must navigate these local requirements to ensure compliance. In Texas and Louisiana, where hurricane resistance is crucial, metal building systems must adhere to stringent wind load standards.
Environmental impact assessments are often required, especially for larger projects. Commercial steel buildings may need to incorporate energy-efficient features to meet local green building standards.
Fabrication and Delivery
Once designs are approved and permits secured, fabrication begins. Steel building systems are often produced in controlled factory environments, ensuring precision and quality. The production timeline for prefabricated metal warehouses in Louisiana is typically shorter than traditional construction methods.
Coordinating the delivery of components is a critical step. For large projects like industrial warehouses, this may involve multiple shipments carefully timed to align with the construction schedule. Metal warehouse building systems are often delivered as complete packages, streamlining the on-site assembly process.
Assembly and Installation
Proper site preparation is essential. For steel warehouses in Louisiana, where soil conditions can be challenging, extra attention is given to foundation work. Commercial metal warehouses in Oklahoma often require extensive groundwork to ensure stability and longevity.
The assembly of steel and metal building systems is where efficiency truly shines. Warehouse steel frames are typically erected quickly, with pre-engineered components fitting together seamlessly. Where speed is of the essence, steel warehouses can be assembled in a fraction of the time required for traditional construction.
Final Inspection and Quality Assurance:
Once assembly is complete, a thorough inspection is conducted. Metal building companies often provide comprehensive quality assurance checks to ensure every aspect of the structure meets or exceeds industry standards.
Regional Nuances
In Texas, the demand for "warehouse metal buildings near me" has led to a surge in local suppliers offering rapid construction solutions. Louisiana's unique climate has spurred innovations in warehouse building solutions, focusing on moisture resistance and hurricane preparedness.
Arkansas has seen a rise in the popularity of custom metal warehouses, with businesses seeking tailored solutions for their specific industries. Oklahoma's diverse economic landscape has driven advancements in metal warehouse design, creating structures that are both functional and aesthetically pleasing.
The construction and installation process for steel and metal warehouses is a testament to modern engineering and efficiency. From the initial planning stages to the final quality checks, every step is designed to deliver a superior product. Whether you're considering steel warehouse construction in Arkansas or exploring pre-engineered metal building systems in Louisiana, understanding this process helps ensure your project's success.
As the industry continues to evolve, with new technologies and materials emerging, the construction process for steel and metal warehouses will only become more efficient and sophisticated. This ongoing innovation ensures that businesses across Texas, Louisiana, Arkansas, and Oklahoma will continue to have access to state-of-the-art industrial and commercial spaces, driving economic growth and operational efficiency for years to come.
Cost Considerations: Maximizing Value with Metal Warehouses
When investing in steel warehouses or metal warehouses, understanding the cost factors is crucial for businesses. Many considerations influence pricing. Here’s how to plan your budget effectively.
Size and Complexity
The scale of your project significantly impacts costs. Larger steel warehouses naturally require more materials and labor. Complex designs, like those often seen in custom steel warehouses, can increase expenses due to specialized engineering requirements.
Material Quality
High-grade steel used in industrial steel building systems may cost more upfront but offers superior durability and longevity. Metal warehouse suppliers can provide options ranging from standard to premium materials, allowing you to balance quality and budget.
Custom Features and Add-ons
Additional features like advanced insulation systems in metal warehouses or specialized doors in commercial metal warehouses can affect the overall cost. However, these investments often lead to long-term savings in energy efficiency and functionality.
Budget Planning Tips
Consider long-term value: Pre-engineered metal building systems may have higher upfront costs but offer savings in maintenance and energy efficiency.
Factor in site preparation: Steel warehouse construction may require additional groundwork, impacting overall costs.
Explore prefab options: Prefabricated metal warehouses often provide cost-effective solutions without compromising quality.
By carefully considering these factors and exploring various options from warehouse metal building systems companies, businesses can make informed decisions that balance cost and value. Remember, investing in quality steel building systems or metal building systems is a long-term investment in your business's future.
The Game-Changing Benefits of Steel & Metal Warehouses
As we've explored the world of steel warehouses and metal warehouses, it's clear that these structures offer a multitude of benefits for businesses of all sizes. Metal building manufacturing offers key advantages.
Durability and Strength: Steel building systems and metal building systems provide unmatched structural integrity, capable of withstanding harsh weather conditions and heavy loads.
Cost-Effectiveness: From prefabricated metal warehouses to hybrid steel warehouses, these structures offer excellent value for money in both short-term construction and long-term maintenance.
Flexibility and Customization: Custom steel warehouses demonstrate the incredible adaptability of these systems, allowing businesses to tailor their spaces to specific needs.
Energy Efficiency: Advanced insulation options and cool roofing systems contribute to significant energy savings, particularly important in the varied climates of the Southern United States.
Rapid Construction: The efficiency of steel warehouse construction and the availability of metal warehouses showcase the speed at which these buildings can be erected.
Scalability: As demonstrated by industrial steel building systems, these structures can easily accommodate future expansions and modifications.
Encouragement to Consider Steel & Metal Building Systems
Given these substantial benefits, we strongly encourage businesses to consider steel and metal building systems for their next construction project. Whether you're in need of expansive industrial warehouses or versatile commercial warehouses, these systems offer solutions that are cost-effective, durable, and tailored to your specific requirements. They offer the perfect blend of strength, efficiency, and adaptability that modern businesses need to thrive in today's competitive environment.
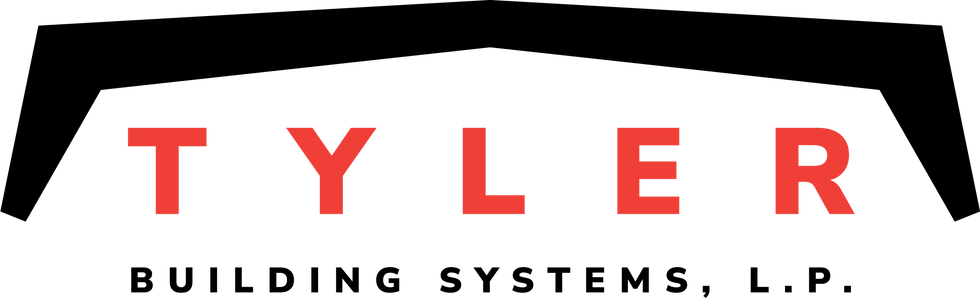
Contact Information for Tyler Building Systems
Ready to take the next step in your steel or metal building project? Tyler Building Systems is here to help. With over 50 years of experience as a metal building manufacturer headquartered in East Texas, TBS has a deep understanding of the unique needs of businesses across Texas, Louisiana, Arkansas, and Oklahoma. The Tyler Building Systems team is ready to guide you through every stage of your project.
Visit tylerbuilding.com to explore a wide range of solutions, from custom designs to pre-engineered options. With experts ready to discuss your specific needs, Tyler Building Systems promises metal buildings made easier.
Start your journey towards a more efficient, durable, and cost-effective building solution. Let Tyler Building Systems be your metal building manufacturing partner.
Comments